当社の技術Technology
冷間鍛造で実現できる4つの価値
冷間鍛造とは、炭素鋼・合金鋼・ステンレス・非鉄金属などの金属素材を金型を用いて圧縮形成される方法で、常温または常温に近い温度で行う鍛造加工を指します。
- 1. コストダウン
- 2. 軽量化
- 3. 強度向上
- 4. 時間短縮
工法転換によるコストダウン
冷間鍛造とは、炭素鋼・合金鋼・ステンレス・非鉄金属などの金属材料を金型を用いて圧縮成形される方法で、常温または常温に近い温度で行う鍛造加工を指します。この加工方法では、高い圧力により材料を変形させて、加工を行うことから、以下のようなメリットがあります。
- 最小限の材料(ニアネットシェイプ)による成形が可能
- 金属組織自体が圧力により収縮し、ファイバーフローが維持された状態を保つために耐摩耗性が向上されます。
また、使用する材料の特徴として、一定の変形性と高くはない変形抵抗を持つことが求められますが、他の鍛造加工と比較して以下のような特徴があります。
- 高い寸法精度を出すことが可能
- 他の鍛造加工と比較して、表面の状態が良好であること
これらの特性を活かすことで、自動車部品等の耐摩耗性や耐久性が必要となる量産品の加工に利用されてきています。現在では、金型の精度の向上により他の加工方法からの工法転換によるコストダウン等の提案が行われています。
コストダウンの実例
1. 切削加工の置き換え
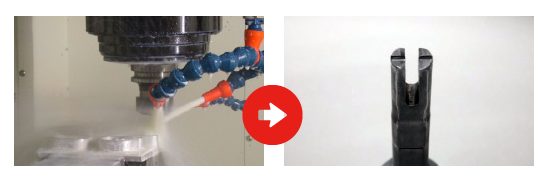
切削加工から冷間鍛造加工への工法転換による最大で1/10のコストダウンを実現!
2. 2次加工レスの実現
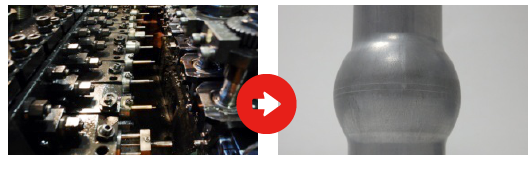
追加工レス化により、最大で1/5のコストダウンを実現!
3. 熱間鍛造加工からの置き換え
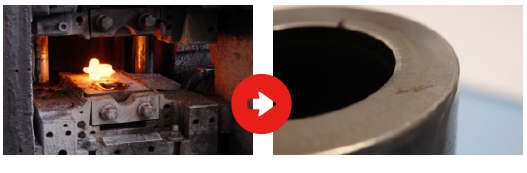
熱間鍛造加工から工法転換によりリードタイム1/5~1/10コスト1/2削減!
4. 既存の冷間鍛造からの工程集約
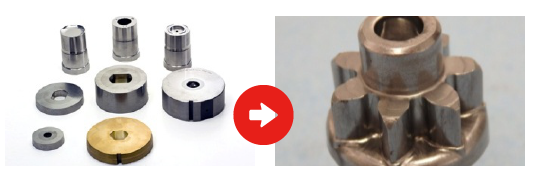
金型の設計変更により冷間鍛造加工に穴加工工程を集約!
冷間鍛造加工による軽量化
冷間鍛造により加工を行う部品はその特性上、硬度と耐久性が求められる量産品の領域で優位性を持ちます。その結果、冷間鍛造加工品の主な納品先としては、自動車業界・エネルギー関連の企業が中心となっていました。
これら業界において近年、エネルギー効率の向上を目的に部品に対する軽量化ニーズが高まってきており、樹脂等の材料変更も行われています。ただし、耐久性が求められる特定の部品に対しては、冷間鍛造による加工品が使用されており、構造上の設計変更による軽量化のニーズが高まっています。
冷間鍛造により取り扱う材料である炭素鋼や合金鋼は、比重が7~9[g/cm3]程度と非常に高いために、細かな設計変更により軽量化を進めることが可能であると言えます。その結果、ボルトやナット等の製品に対して、穴形状や中空構造へと設計変更が行われています。
しかし、これまでの鍛造加工では追加工が難しく、切削等での追加工が主流となっていました。その結果、工程数が増えることによるコストアップにつながっていました。
-従来の鍛造加工における軽量化のためのネック
- 金型設計の設計技術による中空構造・穴加工の形状加工が難しい。
- 切削加工による追加工の為に加工工程が増加する。
近年、金型の設計・製作技術の発展・並びに軽量化ニーズの進行による設計変更が進むことで、冷間鍛造加工の工程における軽量化のための追加工が行われるようになってきています。
当社としても、Tier1クラスの企業からの問い合わせにより追加工の為の金型設計製作を行った事例が多数存在しています。今後も、冷間鍛造加工における中空化・穴加工を含めた追加工ニーズが増えると考えられています。
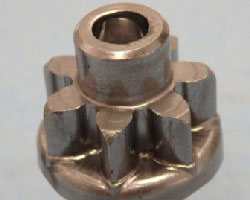
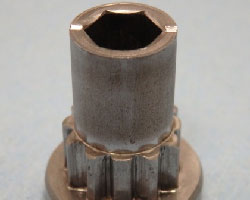
冷間鍛造加工による強度向上
金属の加工においては、加工方法によって同じ材質を使用した場合においても製品の特性に違いが生まれます。特に、金属材料を加工する上では構成する分子の結合により決まる結晶の方向(ファイバーフロー)を考える必要があります。
このファイバーフローというのは金属の靭性に大きく寄与することから、できるだけ切断せずに、活かしたまま使用することが望ましいとされています。
つまり、冷間鍛造による加工は、このファイバーフローを切断しないという点で非常に有効な加工方法であると言えます。冷間鍛造加工の中でも、特に当社が得意とするパーツフォーマーによる成形は非常に大きな圧縮応力を与えて塑性変形させることで、材料が加工硬化することにより機械的性質が変化します。加工度の少ない初期の性質変化が大きく、引張強さ、降伏点、弾性限界、および硬度などは冷間鍛造加工により著しく上昇し、伸びや絞りなどは著しく減少します。
このために、機械仕上後、調質して強度をだしていた製品を冷間鍛造化して硬度の上昇をはかり、調質作業とそれにともなう研磨作業を省略することができたり、何らかの理由によって調質のおこなえない製品の強度を冷間鍛造によって上昇させることもできます。
また、冷間加工を受けた製品は組織が微細化し、ファイバーフローが切断されていないことから耐摩耗性も向上します。
しかし、素材の調質状態、加工の度合、加工方法によって同じ材質でも強度が変化し、かつ、一つの製品でもそれぞれの部分によって加工度が違うので、調質によって得られるような均一な硬度の向上は望めないという点もあります。製品の強度に対する知識は、成形してみてわかるもので、はじめから予測することは豊富な経験をかさねないかぎり非常に困難なことです。
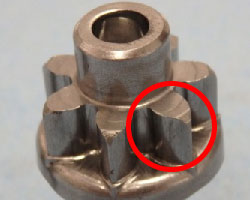
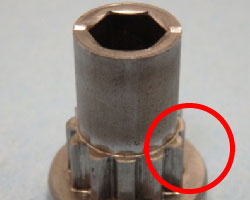
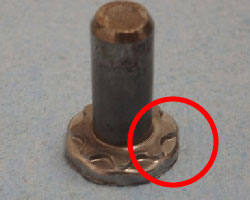
歯車構造は、耐摩耗性が求められるので冷間鍛造による加工を行うことで耐久性の向上につながります。
冷間鍛造加工によるリードタイム短縮
冷間鍛造加工では、製品図面に対して圧造製品形状の決定から工程レイアウトの決定・加工方法の選択を行い、金型設計製作・製品加工・生産ラインの構築へと入っていきます。この過程において冷間鍛造加工による加工領域を検討し、必要となる材料形状の選定や切削加工による追加工を行うことになります。
しかし、炭素鋼やステンレス鋼等の材質の形状指定によっては調達が困難であり、リードタイムがかかってしまうことが懸念されます。
つまり、製品形状の選定もしくは材料指定の段階で調達リードタイムを考慮した設計変更・金型設計が求められます。
当社ではこれまでに特定の形状指定が行われ、冷間鍛造により加工が行われていた製品に対して、独自の金型設計・製作技術により、丸材からの加工へと工程変更によるリードタイム削減を実現してきました。
具体的な事例として以下の様なものが挙げられます。
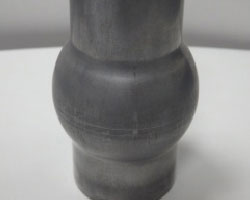
従来:面取り加工を行っていた。
↓金型設計変更により丸材からの冷間鍛造加工へと工法転換 リードタイム1/5~1/10、コスト1/2を実現!
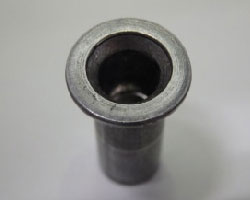
従来:パイプ材を購入後、プレス加工により製作していた。
↓金型設計変更により丸材からの冷間鍛造加工へと工法転換 工程数は1→6と増加したが、リードタイム1/10を実現!
これらの事例のように冷間鍛造加工では、
- 特定の材質形状指定の材料+冷間鍛造加工
- 特定の材質形状指定の材料+その他加工法による追加工